Call us now:
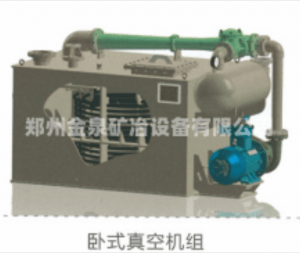
Vacuum unit equipment
I. Equipment Features The vacuum unit is composed of a series of units including anti-corrosion PP water tank, buffer tank, RPP water jet pump, check valve, steam-water jet pump, and
In the ammonia synthesis industry, Ru/C and Ru/MgO catalysts are widely used due to their high catalytic activity and ability to reduce operating pressure and temperature.
Process for treating spent Ru/C catalysts containing Ba and K:
Soak the catalyst in HCl solution for 12 hours to dissolve Ba and K.
Add H₂SO₄ to the filtrate to precipitate BaSO₄ (recovery rate > 87%).
Concentrate the mother liquor to crystallize KCl (recovery rate > 77%).
Incinerate the HCl-leached residue at 800°C for 10 hours.
Mix the ash with an equal mass of KOH + KNO₃ (1:1 ratio), then heat to 650°C and melt for 1 hour.
After cooling, leach the melt with cold water to remove excess potassium salts.
Dissolve the filter residue in hot water (80°C) to obtain a K₂RuO₄ solution.
Add a small amount of NaClO and heat to 60°C for 0.5 hours to oxidize.
Slowly drip concentrated H₂SO₄, then distill under reduced pressure to collect volatile RuO₄ (golden-yellow).
Absorb RuO₄ in 37% HCl solution, then slowly concentrate to obtain RuCl₃·nH₂O (recovery rate: 94.6%).
Alternatively, absorb RuO₄ in HNO₃ solution to produce Ru(NO₃)₃.
Process for treating spent Ru/MgO catalysts containing Ba and Cs promoters:
Dissolve Ba and Cs with 1 mol/L HNO₃ (dissolution rate > 97%); Ru/MgO remains undissolved.
Heat with 1 mol/L NH₃·H₂O to 70°C to selectively dissolve MgO, yielding a pure Mg(NO₃)₂ solution (can be converted back to MgO via carbonate for reuse).
The HNO₃-insoluble residue is crude metallic Ru (recovery rate > 94%).
Industries such as chemical catalysis, electronics, and electroplating often use ruthenium trichloride (RuCl₃) directly. Producing RuCl₃ from spent Ru-containing catalysts simplifies the process, reduces reagent consumption, and improves recovery rates.
Example process for producing reagent-grade RuCl₃ from Ru-containing waste (67.9% Ru, with Pt, Ag, Pb as main impurities):
Place the waste in a distillation reactor.
Add a 30% NaOH solution (5 times the mass of the waste) in three batches while introducing Cl₂ for oxidative distillation (reaction: Ru + NaOH + 4Cl₂ → RuO₄ + 8NaCl + 4H₂O).
Use a water absorber (1st stage) to prevent salt splashing, followed by seven串联 stages of 6 mol/L HCl + 0.5% C₂H₅OH solution to absorb volatile RuO₄ (reaction: 2RuO₄ + 20HCl → 2H₂RuCl₅ + 8H₂O + 5Cl₂).
Filter the 2nd-stage absorption solution, then slowly concentrate to a syrup-like consistency.
Dry gently under infrared light to obtain RuCl₃, then seal (to prevent moisture absorption).
Add ethanol as a reducing agent to the primary distillation residue, let stand for 12 hours until colorless, then filter.
Treat the remaining residue with HNO₃ to separate Ag and Pb.
For the residue (~19% Ru), mix with NaOH and NaClO₃ (mass ratio 3:1:1), then melt at 700°C for 1 hour.
Pour the melt into cold water for secondary oxidative distillation to recover additional RuCl₃.
The final residue contains minimal Ru.
Total Ru recovery rate: 98%.
I. Equipment Features The vacuum unit is composed of a series of units including anti-corrosion PP water tank, buffer tank, RPP water jet pump, check valve, steam-water jet pump, and
Jinquan Electrochemical Deposition Equipment The electrochemical deposition system has revolutionized traditional metallurgical processes through dynamic flow field control technology and is widely used in
Intelligent gold electrolysis equipment combines automatic control, intelligent monitoring and efficient electrolysis technology. It can process raw gold materials with a purity of more than
Jinquan Electrolysis - Cyclone Electrowinning Equipment Cyclone electrowinning equipment is widely used in gold plating solution, gold stripping solution, gold ore heap leaching, spraying solution